Mutable Instruments Rings クローンの製作ですが、ここまできていたのに
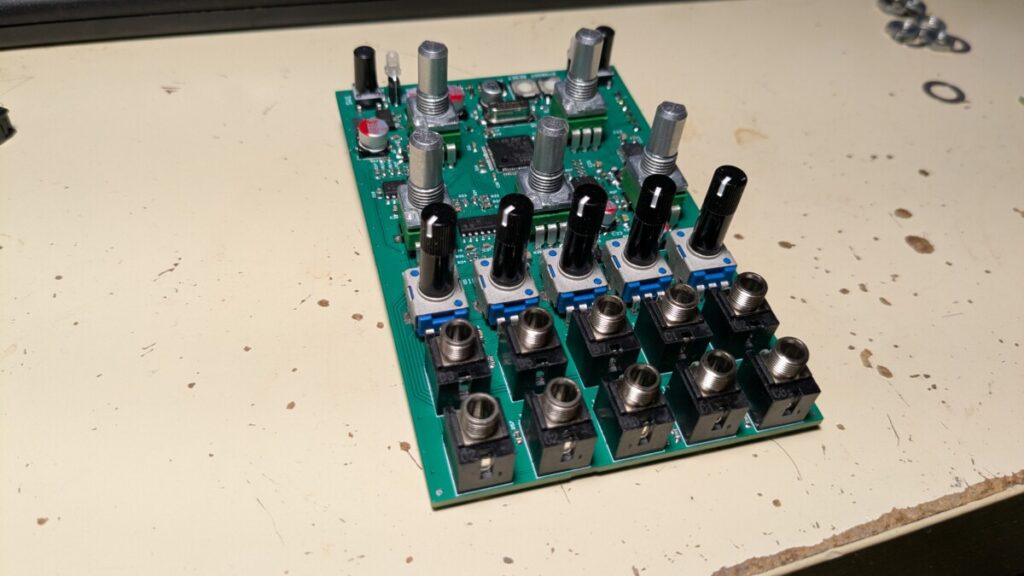
製作が止まっています。どうしたのか?手配するドングルを間違えてファームウェアの書き込みができないんです。ファームウェア書き込みは後日記事にしようと思いますがそれはさておき、実は Rings は二台作るつもりで部品がもう一セットあるので、二台目も作り始めてしまうことにしました。二台目は少し慎重に、ピッチの狭い IC だけホットエアガンで取り付けて、他は手はんだで行こうかと思います。
というわけでこの記事は 0.5mm QFP をホットエアガンで取り付ける二度目の挑戦の話です。また結構失敗して gdgd、冗長かもしれませんけど失敗例も情報かもということで書いてしまいます。
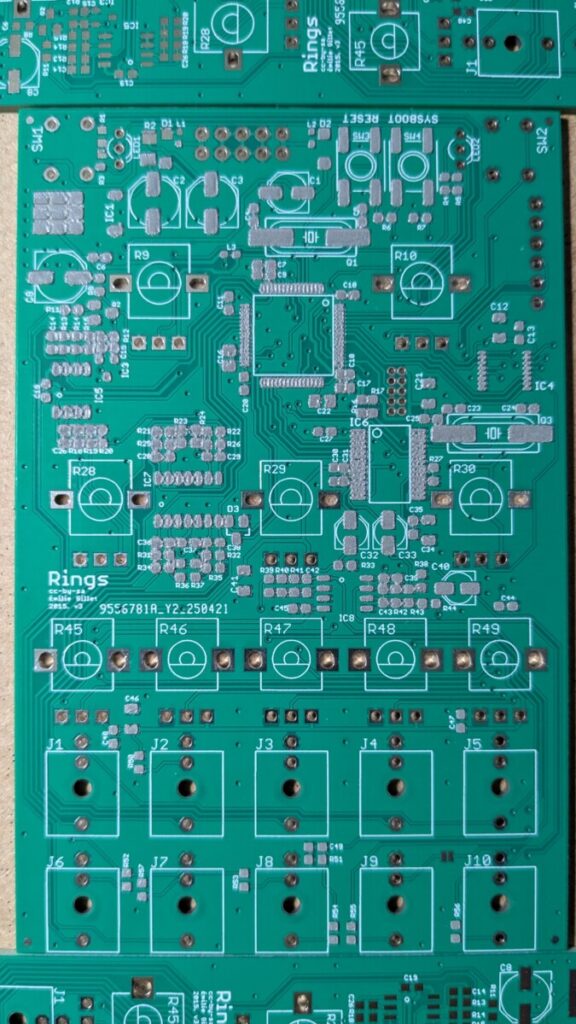
さて今回もステンシルを使ってはんだ付けしますが、左は前回のステンシル作業の結果の写真。ピッチの狭いところでペーストが隣のピンとかぶってしまい、取り付けの時ブリッジしまくりで大変苦労しました。これはやり方が悪かったに違いないと調べたところ、ペーストを平たいプラスチック片で伸ばすとき、ピンの上で何度も伸ばすとこうなってしまう、ということがわかりました。
はい、心当たりあります。四、五回はやりましたよ。今回は一度で伸ばすことを心がけます。
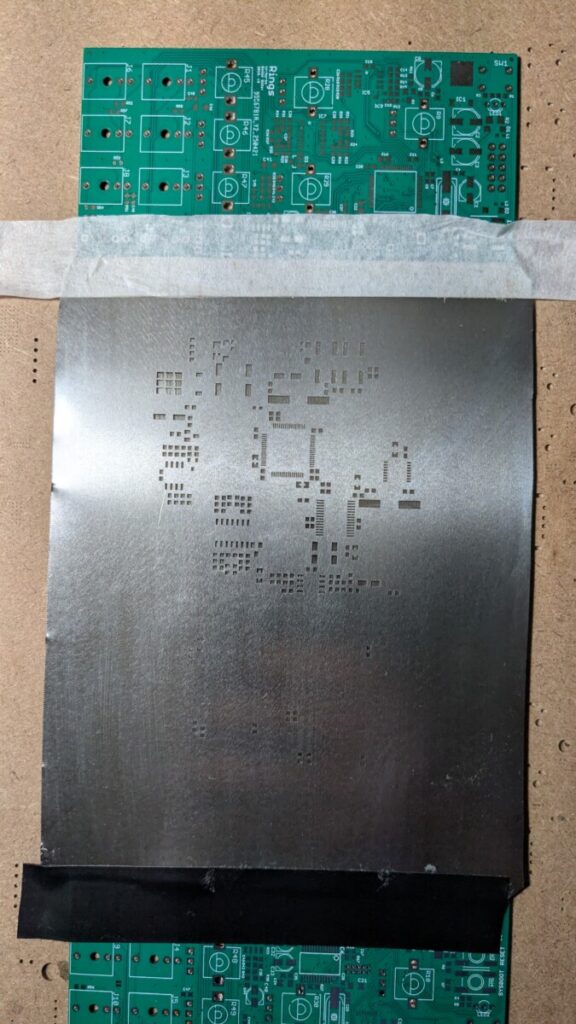
さあ、半田ペースト塗りから再挑戦です。まずは前回同様基板を三枚並べて段差をなくして真ん中の基板を使います。
前回ステンシルを外す時、ぶれずに持ち上げるのが難しかったので今回は下側はしっかりとビニールテープで固定しました。上側はマスキングテープです。外す時はマスキングテープだけ外して上辺だけ持ち上げると簡単にきれいにステンシルが外せます。
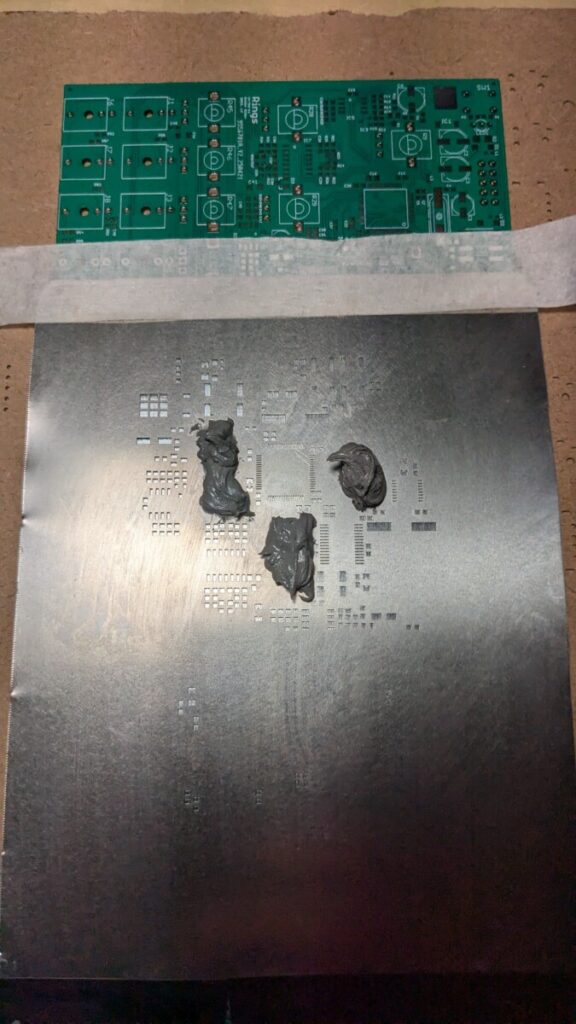
何度か失敗してやりなおし、コツはのせるペーストの量をケチらないことだということがわかってきました。一見もったいないですが余ったペーストはほぼ全部容器に戻せるのでじゃんじゃんいって大丈夫なこともわかりました。
ちなみに、ここの工程は失敗しても基板を洗ってやり直せるのでへまっても致命傷にはなりません。ペーストはじわじわ減るんですけれども。
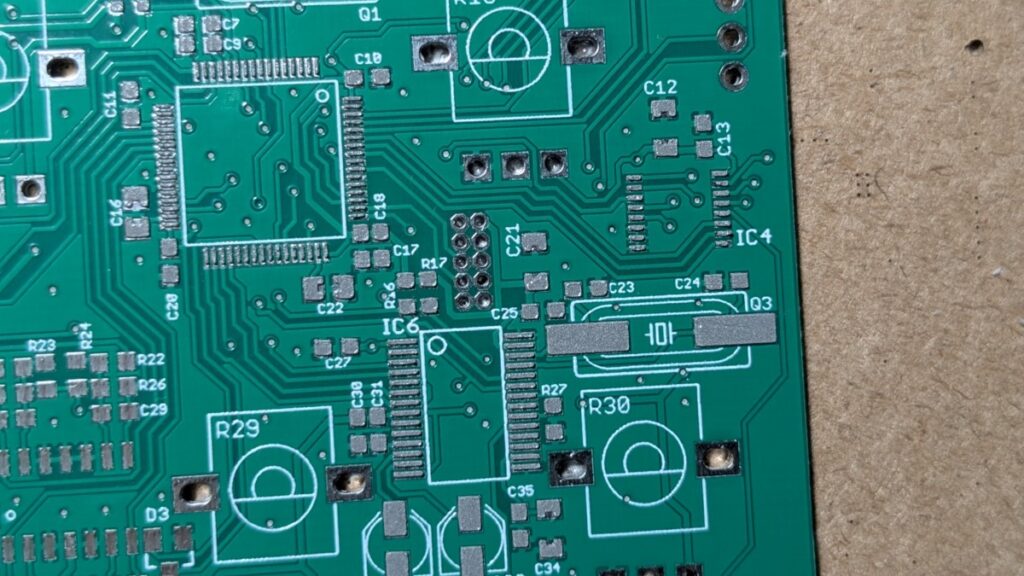
ペースト塗りできました。左上の 0.5mm QFP が若干にじんでいますが前回より全然ましです。0.65mm ピッチの IC4 と IC6 は見た感じ問題なさそうです。うまい人が見たらあごが落ちる問題がありませんように。
まわりの水晶発振子やケミコンの足にもペーストが乗っていますが、ホットエアガンで取り付けるのは大変なのはわかっているので拭き取ってしまいました。抵抗やコンデンサのパッドにも乗っているものがありますがそれは特に困らないのでほっておきます。
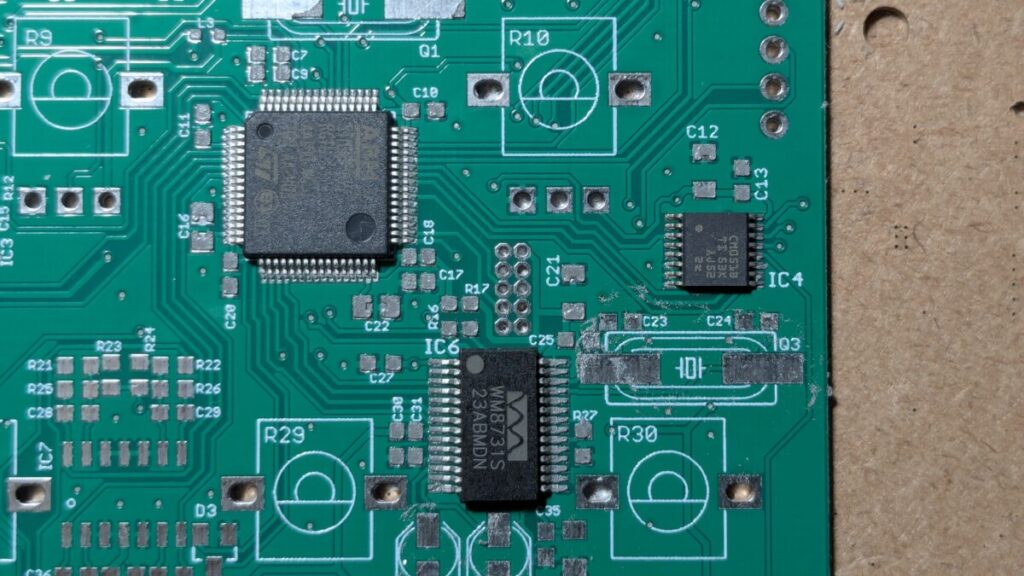
部品を乗せます。ルーペで見ながら慎重に作業しました。
ここでとある大失敗があるのですが作業している本人は全然気づいていません。位置合わせそのものはこれで OK でした。
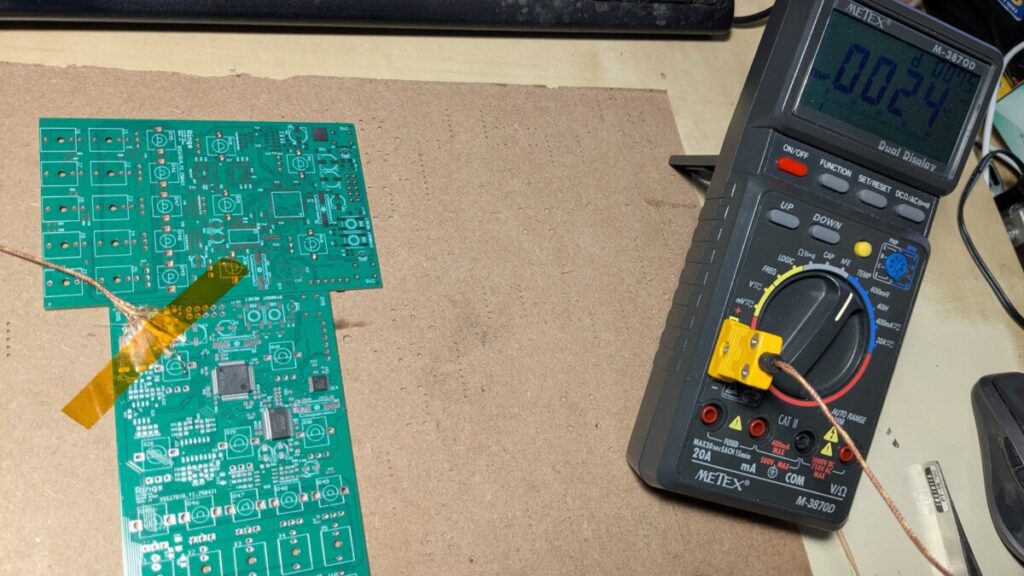
次はホットエアガン作業です。ここも前回要領が悪くて手こずったところ。この工程では熱しすぎて部品を壊してしまうのではないかと心配になるので下調べしました。
ドレメルのガス式ホットエアガンは温度調整ができないのが不安なのですが、調べてみたら温度調整付きであっても吹き出し口の温度と基板の温度はかなり違うとのこと。じゃあどうするの?温度を測りながら作業するのが良いようです。幸い僕のテスターは温度プローブと温度測定機能が付いているので活用します。どれぐらい正確に測れるのかわかりませんが温度計があると心理的には断然楽です。プローブはポリイミドテープで固定。
ちなみにポリイミドテープはホットエアガンが部品のプラスチックを焼かないように保護するのにも使えるとのこと。なるほどです。あと、温度プローブはできるだけチップに近づけるのが良いようです。最終的には写真よりさらに近づけました。
温度を測るのは良いけれどもその温度はどんな風に運用したら良いの?ホットエアガンではんだ付けするときには基板をプレヒートするのが大事らしく、でもどれぐらいの速さで何度まで上げればよいかわかりません。またネットを徘徊、スズ 63% 鉛 37% 半田のリフロープロファイルが kester.com さんのサイトで見つかりました。今使っている半田は kester 製ではないけれども Sn63/Pb37 なのできっと同じような特性でしょう。kester さんありがとう!
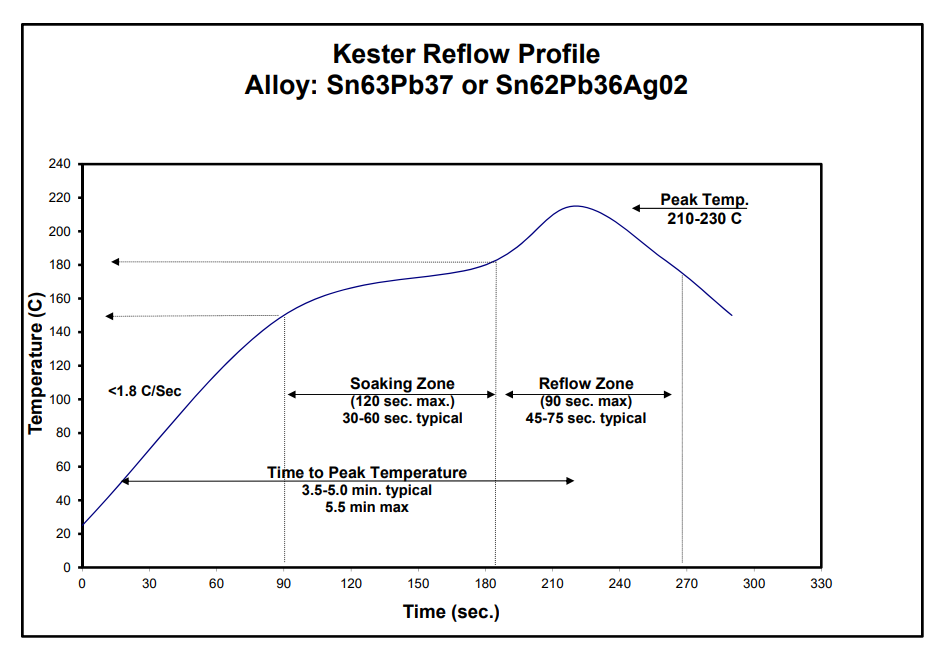
このチャートと温度計とストップウォッチとにらめっこしながらゆっくり温度を上げて行きはんだ付けします。たしかにやみくもに熱風をかけるよりずっと安定してはんだ付けできました。スマホをストップウォッチとして使っている間カメラとしては使えないので写真は撮れずです。
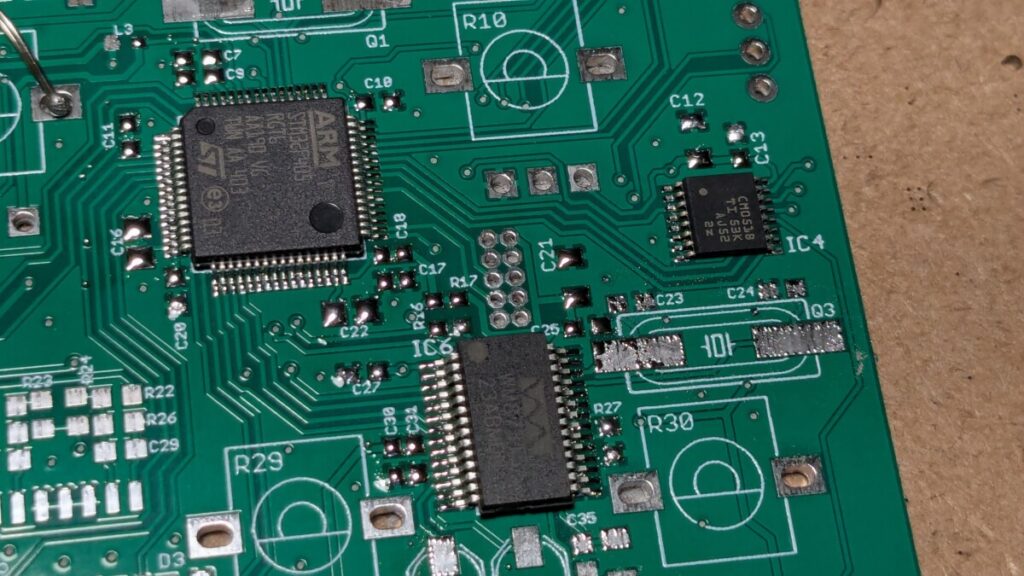
ホットエアガンを吹き終わったところ。ぱっと見ブリッジらしい部分もほぼ見当たらず、前回よりもきれいについています。
が、ここで重大な間違いに気づきます。プロセッサの向きが間違ってます。位置合わせは良かったけど向き合わせがダメでした。僕はバカなんでしょうか?
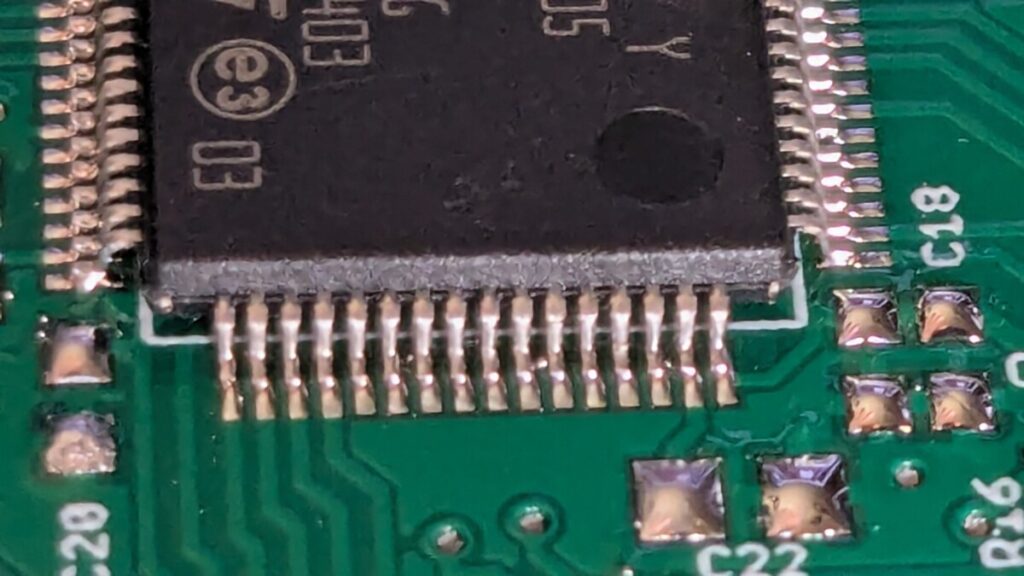
こうなったら取り付けなおすより仕方ありません。
チップを外す前のはんだ付けの状態。結構きれいにつけられたと思ったのに。悔やまれます。
部品がきれいに外せるか心配でしたが基板をきちんとプレヒートすると意外とすんなりと外れてくれることがわかりました。
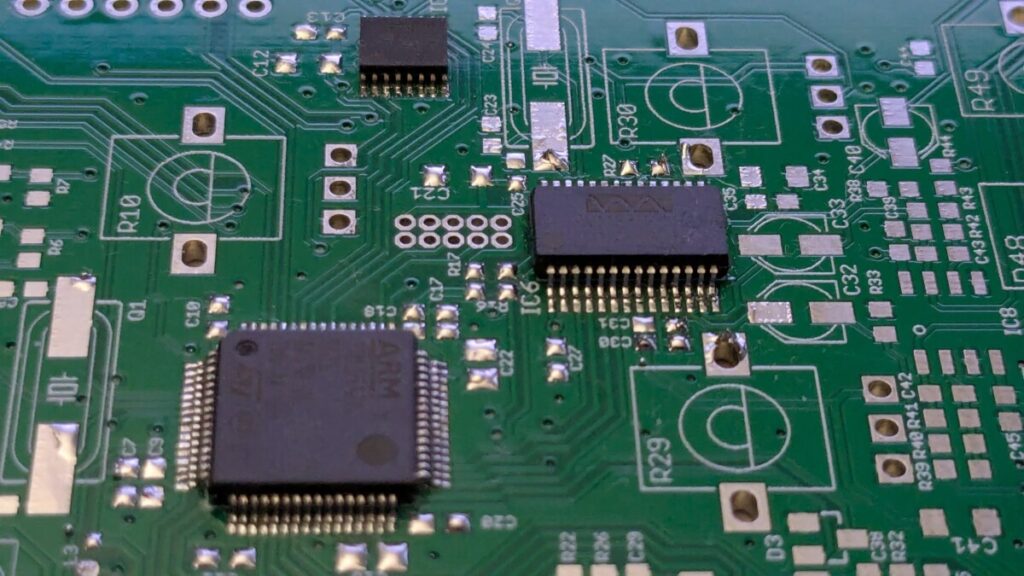
チップの向きを直して再度ストップウォッチと温度計とチャートを睨みながら部品を取り付け、一度目ほどはうまく行きませんでしたが半田ごてでブリッジや接触不良を修正して無事に部品が付きました。修正中、半田が足りなくなって追い半田が必要でした。今までずっと半田は減らす苦労をしてきましたが増やすのが必要になったのははじめて。
ほかのチップも半田ごてで若干の修正が必要でした。
導通テストが完了して、フラックスを洗浄して、チップのはんだ付け作業はここまでです。
半田ごて作業なくホットエアガンを使って一発でばちっと決められるようになりたいです。でも 0.5mm ピッチはいまだに地獄ですけれども 0.65mm はなんとなく怖くなくなってきました。
以下参考資料です: